DICOM to STL? Patient-specific printable 3D models
Additive manufacturing and 3D modelling have significant and increasing value in patient-specific surgery planning and medical education. As we faced projects requiring such operations, we know that it is not only about a personalized treatment approach, but also usually personalized and manual work over the whole process from DICOM to STL. Often to achieve satisfying results companies are in need of utilizing different tools and software. We believe there is a simpler way. In this post we’d like to show you how we approached technological obstacles and enabled our clients to quickly produce their own accurate 3D models in an automated manner.
Technology to solve most problems in 3D modelling & printing
DICOM – Digital Imaging and Communications in Medicine [1] files contain vast amounts of data and information. The initial step but also probably one of the most critical steps here is a precise segmentation of the object of interest. The smaller it is, the more complex the task becomes – especially if manual segmentation is involved.
Converting DICOM images of cerebral aneurysms into STL format for 3D printing is a complex process. We faced the task of software development that would facilitate STL file preparation for cerebral aneurysms. Vessels segmentation (segmentation of vascular system in general) is highly time-consuming, however, thanks to our internal RnD projects we managed to propose an algorithm that performs it automatically.
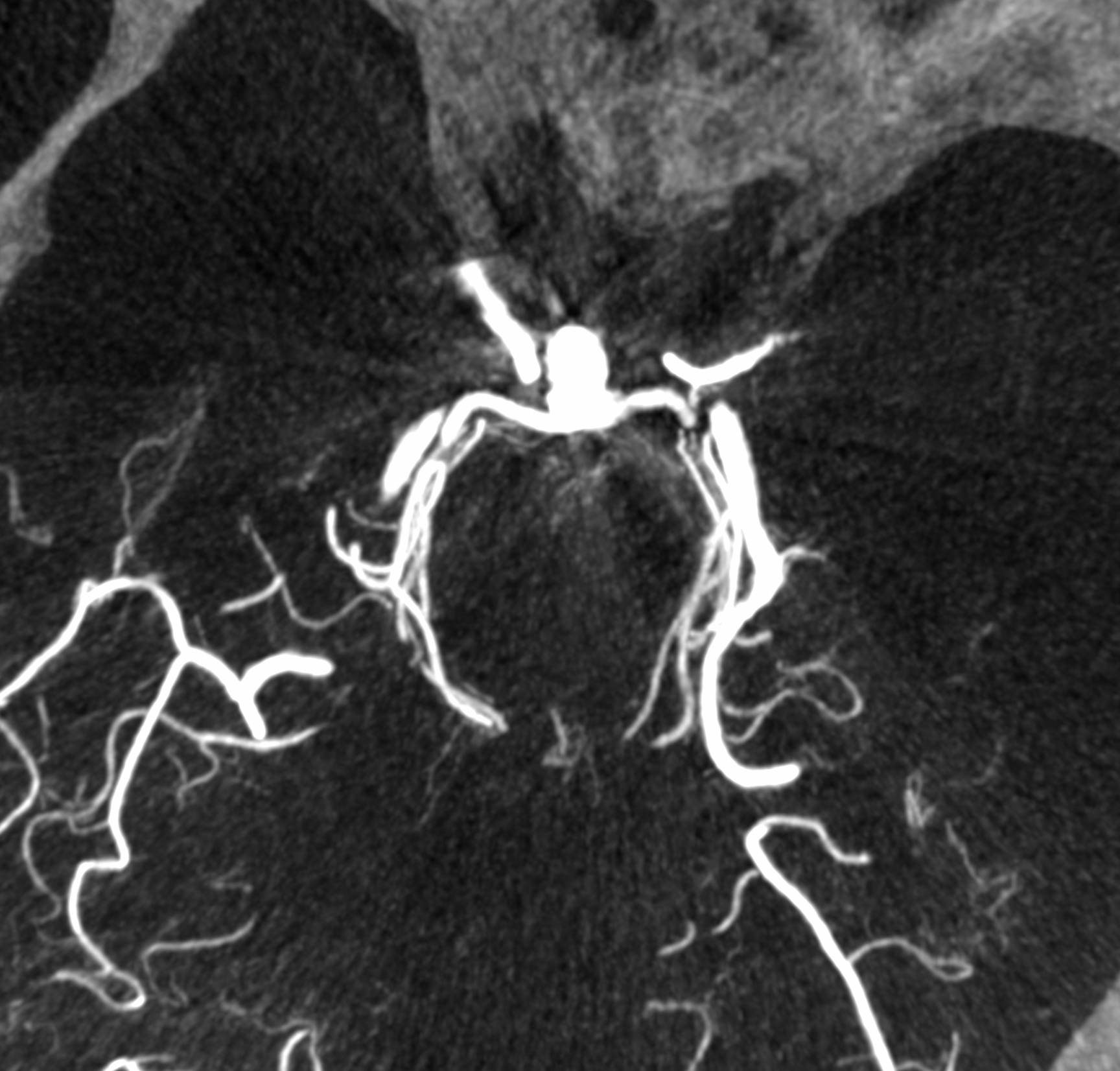
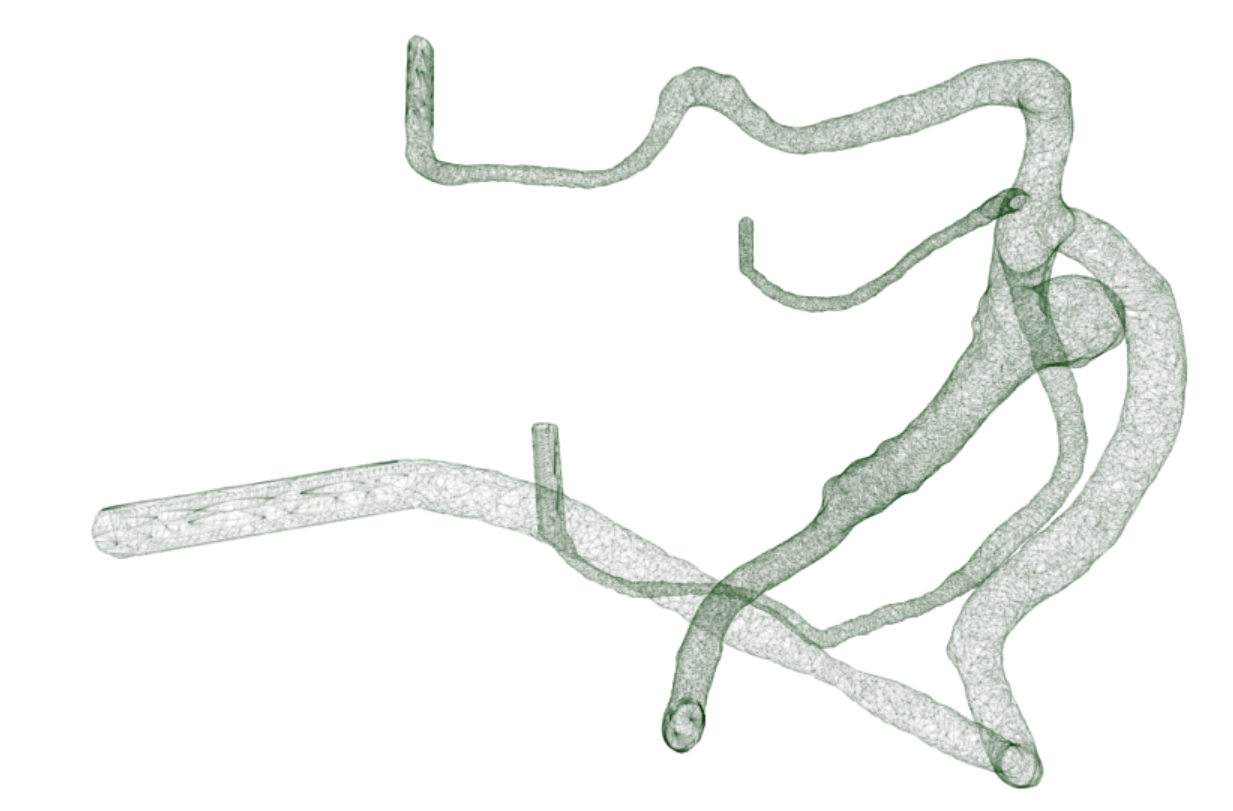
Medical evaluation of segmentation accuracy was positive. Mesh of micro-triangles with vessel diameter being up to 5 [mm] – built upon this segmentation – was an input to the further steps. Each of them is described in detail in separate posts, below you may find general descriptions and links.
Printable 3D models of brain aneurysm – required steps
The task was to automatically connect the inflows and outflows of a segmented 3D model of a brain aneurysm to points in well-defined location 3D space to produce a physical 3D printable model. We began by calculating the model’s centerlines, which provided us with information about the presented mesh, such as diameters along the centerline points. The mesh was then divided into separate branches so that we could determine which part of the mesh was an aneurysm and which part was a model ending. Then we proceeded to the automatic connection optimization phase, where we decided which point to use for cutting the branch and connecting it to the 3D point in space. As a result, we successfully created automatic and seamless connections for the brain aneurysm mesh.
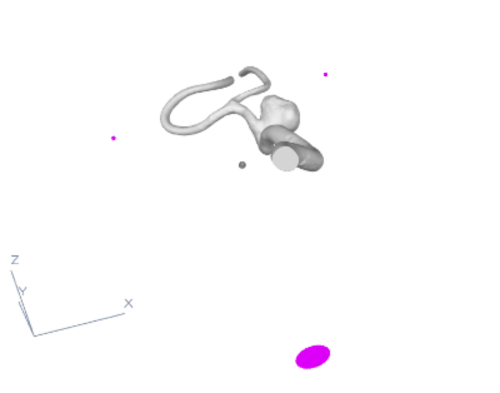
3D models: mesh seamlessly connected to the original anatomy
The next step was not any easier. The team’s challenge was to generate the actual mesh and seamlessly append it to a model. There was one more important requirement for these connections. They should not only be smooth in terms of starting and ending vectors, but the generated 3D mesh should also be seamlessly connected to the original anatomy. This means it should begin with the exact contour of a branch cross-section and smoothly transition into the desired circular shape. We described this in detail in a dedicated blog post about generating smooth connections in 3D mesh models of brain arteries.
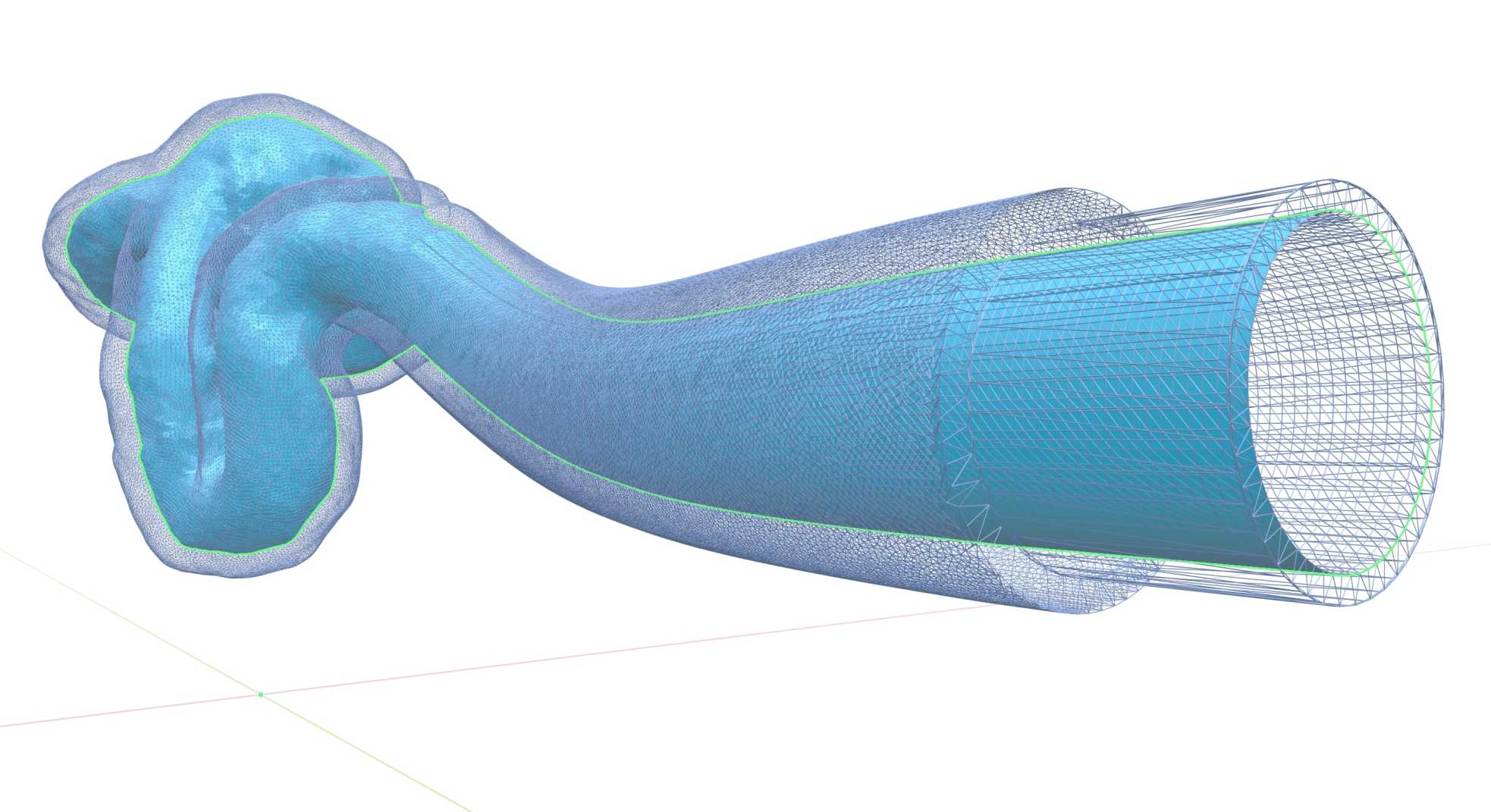
In another step we used all the previously developed algorithms and faced the challenge of creating walls around the 3D model that had a pre-set thickness over the entire volume, without changing the anatomy relative to the initial model, to ensure the mechanical properties of the resulting printout – all that in a fully automated manner. The process had to provide a certain target shape for further tight placement in the physical flow simulator as well. Discover more about the challenge of optimizing connections between the vessel model and 3D printable models.
We also worked on and solved other issues that arose during the project. For instance, we developed an iterative algorithm that is resilient to the majority of issues encountered in the practise of precisely preparing geometry for 3D printing.
Finally, our client received an automated solution to solve complex problems that would have previously required sophisticated CAD tools and a qualified technician.
3D modelling and printing in medicine
Although the use of 3D printing in medicine is an inspiring direction, it often still remains in the area of research and development. Working on patient-specific models frequently necessitates extensive knowledge from various areas of specialization as well as expertise in conducting research projects. We have proven experience in both cases and can assist you.
References: